Zhongding has deep cooperation with Southeast University to jointly design and develop a variety of fluidized bed drying and incineration technology, and provide professional one-stop solutions of sludge drying, sludge incineration and sludge recycling treatment. The company also has a number of inventions and utility model patents. Our drying and incineration technology has been successfully used in a number of projects, solving the challenges of difficulties, pollutions and high costs associated with sludge drying and sludge incineration treatment, while also avoiding secondary pollution. This resulted in a breakthrough progress for China's sludge treatment and disposal technology.
The company always adheres to the concept of continuously creating value for customers. Our technical equipment will be developed, manufactured and configured specifically according to the actual situation of different projects, ensuring long-term stable operation with low cost and high yield.
Features of Sludge Drying & Incineration Technology
- Able to handle feed sludge with wide range of moisture content
The sludge drying and incineration system can dispose of various sludge raw materials, including municipal sludge and industrial sludge. The highest moisture content of feed sludge can reach around 80%.
- Safe drying with high temperature
The full utilization of drying technology helps effectively avoid sludge powder explosion and improve the safety and reliability of the system.
- Efficient, energy-saving drying & incineration process
The adiabatic furnace ensures self-sustaining incineration of low calorific value sludge, and a heat value of 1000 kcal can ensure self-sustaining incineration above 850 ℃ without the addition of auxiliary fuel. Fully utilizing the system's waste heat, the boiler outlet flue gas temperature is around 200 ℃, achieving the most efficient energy conservation and environmental protection.
- Multiple types of equipment to meet various requirements
Non-standard customized design is available to meet various small, medium, and large sludge treatment projects.
Process diagram of sludge disc drying & incineration system
Process diagram of sludge rotating airflow bed drying system
Sludge Disc Drying & Sludge Disc Drying System
- The disc drying system consists of main functional components including main body, hollow shaft, drive unit, material outlet device, electrical control, etc. The entire system is featured by high efficiency and low cost.
- It can handle various types of sludge with a moisture content ranging from 80% to 60%, and the moisture content of the discharged sludge ranges from 30% to 40%.
- The steam and sludge in the drying system are in full contact, and the entire system is fully enclosed, with high safety.
- Compact structure and small footprint of the device; Low oxygen content, temperature, and dust concentration during operation. There is a special scraper designed on the inner wall of the shell, which can fully mix materials and clean the disk surface.
Sludge Rotating Airflow Bed Drying System
- The flue gas leaving the incinerator, at about 800 ℃, is tangentially fed into a cyclone horizontal dryer. The wet sludge is stirred (or pumped) into the dryer and collides with the high-temperature and high-speed rotary drying medium that enters in the tangential direction, causing it to become particulate and present in a fiercely swirling state. The larger and more sticky wet sludge is dried while being flipped upwards by the drying and stirring device installed in the middle of the dryer. It has good contact with high-temperature hot flue gas, and the water in the wet sludge quickly evaporates and dries.
- The dry sludge particles that reach a certain dryness are carried out of the dryer by the airflow and enter the vertical drying tower. After further drying, they enter the capture system and are captured. The wet gas leaving the capture system is sent through the flue gas treatment system and discharged into the chimney by an induced draft fan.
- Good airtightness, no increase in oxygen content during the drying process, almost the same as the oxygen content in the flue gas (about 5%), eliminating the possibility of sludge deflagration during the drying process.
- The high-speed rotating airflow has a strong scouring effect on the wall surface of the drying tower, reducing the possibility of sludge sticking to the wall. The rotation of the stirring blades causes a small amount of sludge adhering to the tower wall to undergo cutting action and fall off.
- Due to the small volume of the core equipment of this system, the rotary spray dryer, and the relatively simple system, the overall structural volume is relatively small, and the initial investment in civil engineering and construction is correspondingly reduced, making installation and maintenance convenient. Due to the small size of the drying equipment, the heat dissipation and leakage heat loss are small, and the heat utilization rate is high.
Appearance of sludge before and after drying
Sludge with 80% moisture content
Sludge with 40% moisture content
Sludge with 30% moisture content
Self-Sustaining Combustion Fluidized Bed Sludge Incinerator
- Unique design of fluidized bed furnace achieves stable combustion of sludge with heat down to 1000kcal, eliminating the need for additional auxiliary fuel.
- Combustion reaches a temperature over 850℃ and the thermal gas maintains for at least 2 seconds to decompose organic matters. It can work with flue gas treatment equipment to ensure ultra-cleaning of flue gas emissions.
- The fluidized bed incinerator features multiple points of entry to allow multiple materials feeding, thus achieving co-combustion modes for dealing with various materials simultaneously.
Before and after incineration
Sludeg with 40% moisture content
-
Slag
Bottom ash
Team of Experts
-
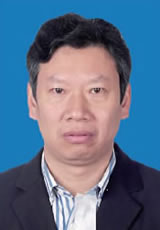
-
Dr. Shifu Ge
Professor of Southeast University
He has achieved fruitful results in sludge drying and incineration field
-
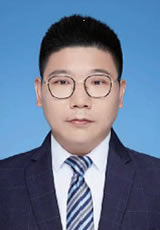
-
Dr. Meng Liu
Doctor of Southeast University, thermal engineering scientist Specializing in dry pyrolysis carbonization and engineering application
-
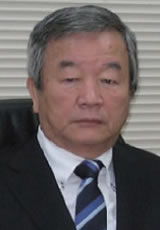
-
Mr. Kawazu
Japan's leading expert
He has more than 40 years of design, development and manufacturing experience in the environmental protection field
We are delighted to show some of projects we have executed
Discover Our Complete Systems
Zhongding is a company with focus on the design and manufacture of incineration systems and waste treatment equipment for various industries. We have different waste disposal systems for global incineration plant operators and waste treatment companies, such as rotary kiln incinerators that are used to handle industrial, medical and hazardous wastes, and sludge incineration systems that can accomplish sludge drying and incineration processes. In addition to providing turnkey solutions for hazardous waste handling and sludge treatment, we also supply waste handling equipment like baghouse dust collector, filter bag cage and disk feeder to help waste treatment facilities achieve higher operational efficiency.