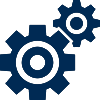
To ensure product quality and engineering quality, we conduct comprehensive inspections of our products according to product drawings and industry standards. In addition to regular quality checks, we also pay attention to the following items (all data is archived for review):
- To establish an effective quality management system throughout the entire manufacturing process, implementing factory-level, workshop-level, and team-level quality management. To strengthen inspection procedures, have qualities of every process under control, prevent unqualified items from entering the next process, and ensure the qualification rate of semi-finished products.
- For major components of the product, quality control points are determined according to the drawings and relevant product standards, based on which inspections will be conducted.
- To strengthen the quality control of raw materials and supporting parts. All raw materials and parts purchased from suppliers should have certificates and warranties. Upon entering our factory, these materials will be sampled and tested by our dedicated inspectors. Only materials that pass the inspection can enter our warehouse for production. For supporting equipment such as motors and reducers, we will arrange professional personnel for testing and trial operation.
- To strengthen product assembly quality control.
Products should be assembled strictly according to drawings and assembly process requirements. For components need to be assembled in factory, they must be debugged in factory, while strict quality control management is conducted. They’ll be shipped from the factory only after passing the inspections.
For components that need to be assembled on-site, they must be debugged in the factory first. They’ll be assembled on-site only after passing the inspections. - To strengthen paint quality management. Our structural parts are coated with anti-rust paint after shot blasting and rust removal, ensuring a anti-rust capability durable for over 6 years. The product will be shipped from the factory only after passing the inspections.
- To strengthen delivery quality control. Products will be packaged according to drawings. Before delivery, all products and accessories will be checked, and defective components will be replaced. For qualified products, the delivery procedure will be carried out, a certificate of conformity for the product will be issued.
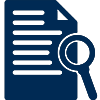
- All equipment designs undergo continuous improvement and optimization to strive for perfection. Manufacture and inspection are conducted according to standards (for process and quality) required by our cooperating experts from Japanese institute.
- During manufacturing, customer can send representatives for monitoring. If quality issues are found, customer has the right to inform us of details and request remedial measures. Equipment that has been reworked, must be deemed reusable and issued approval documentation by the customer before proceeding to the next step.
- Zhongding is responsible for its product’s quality. Purchased materials, components and equipment should meet design requirements and any special requirements proposed by the customer. Changing on types and specifications of purchased materials and equipment must be approved by customer first.
Zhongding is a company with focus on the design and manufacture of incineration systems and waste treatment equipment for various industries. We have different waste disposal systems for global incineration plant operators and waste treatment companies, such as rotary kiln incinerators that are used to handle industrial, medical and hazardous wastes, and sludge incineration systems that can accomplish sludge drying and incineration processes. In addition to providing turnkey solutions for hazardous waste handling and sludge treatment, we also supply waste handling equipment like baghouse dust collector, filter bag cage and disk feeder to help waste treatment facilities achieve higher operational efficiency.